The photographic hire company Lensrentals had a $2k Sony FE 135mm f1.8 GM camera lens returned with a problem: it was having issues focusing. So, they decided to do the obvious thing and take it apart. It’s a fascinating insight into some of the engineering that goes into a high-end camera lens.
That is perhaps a rather scary thing to do, because this is a very new lens that doesn’t even have a service manual yet. That’s akin to rechipping a Ferrari when you’ve never even opened the hood before.
One of the interesting things inside is the presence of a number of shims that adjust the placement between the groups of lens elements. It seems that however good their manufacturing tolerances are, sometimes you just have to put a shim or two in there to align things.
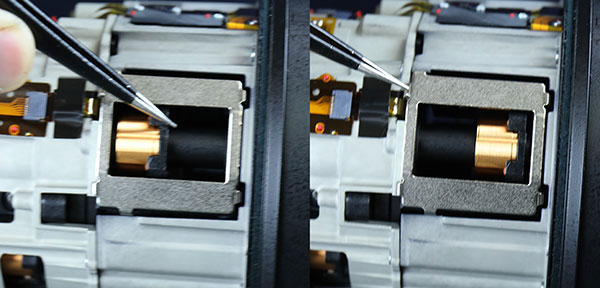
There is also a tantalizing glimpse of the focus mechanism, which slides one of the element groups back and forwards to focus the lens. And again, there are some manual adjustments that are made with screws to keep this group of lens elements aligned.
Unfortunately, Lensrentals didn’t go all-in with the teardown: they stopped when they found the problem, in which a single element had shifted, throwing off the performance of the entire lens. That’s a pity, as camera lenses are a major driver of miniature electric motor innovation, needing as they do to move large groups of elements quickly and very accurately to focus. There is an excellent view of the aperture element though, and it is possible to see how the lens uses twelve metal leaves to create an almost perfectly circular aperture.
This article is well worth a read if you would rather not tear apart your own expensive camera lenses.
There wasn’t much left to disassemble. The aperture mechanism is more or less the same in all lenses (save for the number of blades it drives), and the rear focusing group uses the same type of voice coil, only smaller. They showed the front group and focusing mechanism in great detail. Those who follow their blog will remember the voice coils in the 70-200 and 400 F2.8, and how it compares to the recent Canon 400 F2.8 and other pro lenses that need to move large amounts of glass using more conventional ultrasonic motors.
As for electronics, long gone are the days of lots of electronics spread around the lens. Nowadays, it’s pretty much a single PCB running the whole show, with flexes running the length of the lens to whatever encoder, switch, or motor that needs wires.
I’ve been following lensrentals’ blog for years. There’s a lot to be learned about mechanical design, optics, and general do’s and don’ts regarding disassembling precision gear.
“One of the interesting things inside is the presence of a number of shims that adjust the placement between the groups of lens elements. It seems that however good their manufacturing tolerances are, sometimes you just have to put a shim or two in there to align things.”
A common solution to mixing mass produced parts (Lens Body) and precision parts.(lens elements)
Even larger items follow this path, such as a VW transmission.
The case is hogged out on a large CNC, (Very quickly) and the bearings and gears are the precision parts.
Shims are added after all parts are measured for slack. Production speed is key to profitability.
This applies to even injection pumps. Tolerances between cast and machine parts dictate this type of practice. It’s not a disappointment, but instead a fact if manufacturing using multiple disciplines.
This brings me back to stepper motor discussion and why do we even use them, when we have better solutions, with simpler manufacturing etc
Is a $2k lens really “high end” nowadays?
I’m 50 years old now and my days as a hobby photographer are over; but in my active days “high end” started; inflation corrected; at $15-20k.