[Sam Battle] is no stranger to these pages, nor is his Museum is not Obsolete. The museum was recently gifted an enormous Nixie tube created by Dalibor Farný, a B-grade (well, faulty) unit that could not be used in any of their commissioned works but was perfectly fine for displaying in the museum’s retro display display. This thing is likely the largest Nixie tube still being manufactured; although we read that it’s probably not the largest ever made, it’s still awesome.
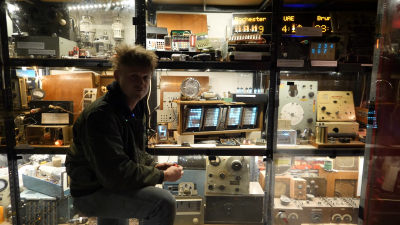
It is fairly simple to use, like all Nixie tubes, provided you’re comfortable with relatively high DC voltages, albeit at a low current. They need a DC voltage because if you drive the thing with AC, both the selected cathode digit plate and the anode grid will glow, which is not what you need.
Anyway, [Sam] did what he does best, clamped the delicate tube in some 3D printed mounts and hooked up a driver made from stuff he scraped out of a bin in the workshop. Obviously, for someone deeply invested in ancient electromagnetic telephone equipment, a GPO (British General Post Office, now BT) uniselector was selected, manually advanced with an arcade-style push button via a relay. This relay also supplies the ~140 V for the common anode connection on the Nixie tube. The individual digit cathodes are grounded via the uniselector contacts. A typically ancient GPO-branded snubber capacitor prevents the relay contacts from arcing over and ruining the display unit. There isn’t much more to it, so if you’re in the Ramsgate, UK, area anytime soon, you can pop in and play with it for yourself.
Nixies are cool, we’ve covered Nixie projects for years, like this DIY project from ages ago. Bringing such things into the modern area is the current specialty of Dalibor Farný, with this nice video showing some of the workmanship involved. By the way — the eagle-eyed will have noticed that we covered this particular Nixie tube before, shown in the format of a large art installation. But it doesn’t hurt to get close up and play with it on the bench.\